In his latest post, Programme Lead Chris Smith PCQI, asks what is root cause analysis and why is it important? He provides a four-step process to ensure you discover the root causes of problems and identify the most appropriate solutions.
What is root cause analysis and why is it important?
Root cause analysis is a process, and the key to success is ensuring it’s controlled by a robust process and creating a positive action plan to prevent recurrence.
Once it is perceived and controlled in the same manner – as other processes in the organisation’s quality management system, it is possible to implement root cause analysis effectively.
Root cause analysis creates the input to corrective action planning by establishing requirements. Without thorough and well-controlled investigation of the root cause of a given problem, any attempt at corrective action is likely to fail. It would be like manufacturing a product without fully developing the specifications needed to fulfil the design requirements.
The purpose of root cause analysis
ISO 9000 describes seven Quality Principles, one of which is: “Evidence based decision making.”
Making decisions is never easy and naturally involves a degree of uncertainty, but ensuring that decisions are based on the analysis and evaluation of data is more likely to produce the desired result. When the data reveals that an area is underperforming, it is important to take corrective actions to improve performance.
As such root cause analysis is an excellent way to determine the source of the problem for knowing what corrective actions should be taken.
Root cause analysis investigates the root cause of identified problems in order to develop and implement a plan for corrective action. Note that the specific intent is to move on to corrective action.
Only those problems and non-conformities that meet the criteria of this evaluation flow through to the corrective action process. It is inappropriate to expend large amounts of money and resources on a situation posing a minimal risk to the organisation. Therefore, since the process that precedes corrective action is root cause analysis, you can conclude that root cause analysis only occurs if there’s been a decision to conduct corrective action.
This distinction should allow you to better comprehend the difference between evaluating a nonconformity and conducting root cause analysis. The former will result in the decision to take some action, such as correction, remedial action, rework, monitoring etc. The latter will result in the identification of the causes of the problem and the development of an appropriate action plan in order to prevent recurrence.
1: Get started with root cause analysis
The first step in this process is to evaluate the situation, the inputs and arrive at a conclusion in order to initiate root cause analysis. The second is to select the members of the team who will conduct the root cause analysis. Giving thoughtful deliberation to the assignment of team members is as important as it is for any other process. It’s important to assign tasks to competent individuals, to communicate expectations and to ensure their availability for the project.
As you begin to select participants, it’s important to communicate the distinction between evaluation and root cause analysis. Otherwise there will be the predictable confusion, with individuals assuming that once they’ve told you that the battery needed to be replaced or a test wasn’t correctly scheduled that their job is done. What they need to understand is that root cause analysis has just begun.
There are myriad tools and techniques available for this process, but not all tools are used every time. In each instance, individuals involved should have the latitude to select the tools that best fit the situation.
In order to maximise the pool of possible candidates to participate, it is most advantageous to use basic, easily learned tools. The fact that they are basic does not diminish their effectiveness. In many instances the basic tools are also the best. Using these tools also serves to increase individuals’ confidence in their ability to make a meaningful contribution. The introduction of complicated tools can alienate people who could otherwise provide valuable input.
2: Examine documentation
Once the team has been assembled, the next step is to examine the evidence that relates to the situation to ascertain the requirements. It is often the case that assumptions are made about requirements that are not substantiated by evidence. This crystallises in the team’s mind what the requirements actually are.
In addition to establishing what the ‘right’ thing is, an evidence review will reveal issues such as:
- incomplete or missing requirements
- requirements not adequately identified.
3: Verification
Now that the team has determined the requirements, it is necessary to verify that they are being fulfilled. Reviewing the evidence allows individuals to prepare questions to ask process owners that will help to verify conformance to the defined requirements.
Verification takes two paths. One is through interviewing, and the other is through looking at records and other evidence. Interviewing will provide information as to the level of conformance to procedures. Are people doing what the procedures say they should? Are they conducting processes in the same manner as described? If there are variations, it is appropriate to investigate further to determine if the variance is part or all of the root cause. Accessing evidence will facilitate this determination.
Flowcharting is often a by-product of interviewing. The process is drawn twice, once as it is prescribed, then again as it is implemented. Comparisons between the two quickly reveal breakdowns. The act of flowcharting also makes process owners think about what they do as they are drawing the flow of activities. This sometimes allows them to pinpoint errors and omissions that show a process to be losing control.
Evidence forms the foundation for root cause analysis. The integrity of the organisation’s information retention practices has direct influence on the effectiveness of this process. Root cause analysis doesn’t begin the day an organisation becomes aware of a problem. It starts months earlier with the aggregation of good data.
Once the interviewing and/or flowcharting processes are complete, the evidence can be accessed to substantiate or refute what has been conjectured as a possible root cause. Training people to do root cause analysis should include guidance on how to access the pertinent information in a timely fashion.
4: Mind maps and ‘Five Whys’
There are two simple tools that help to generate ideas about what could have happened. They are mind mapping and the ‘five whys’. The overwhelming benefit of both of these is that they stimulate our creativity; they get us out of a narrow focus so that we can explore other possibilities.
The results of both of these exercises should be used to populate a cause and effect diagram also called fish bone diagram. This diagram should be used at the most basic level to keep the process simple.
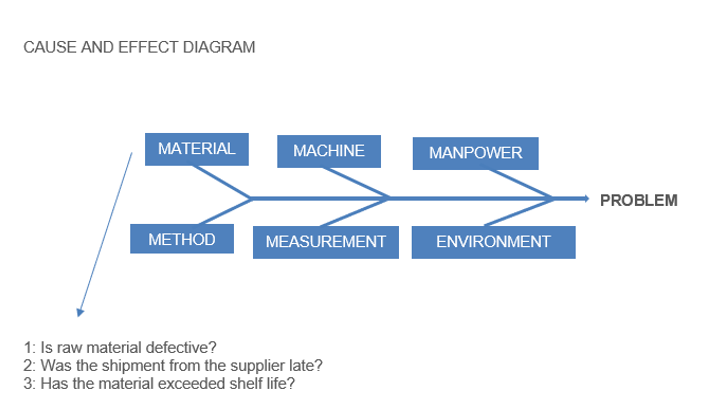
The results of the mind mapping session can be paraphrased as questions and then used to populate the various blocks of the diagram. For example the above diagram shows the material block populated with questions derived from a mind mapping session about late deliveries.
When all of the blocks have been populated with the output of the mind mapping session, the team begins the task of seeking out the records that will provide objective evidence to answer the questions.
The results of the exercise are recorded on a worksheet or brown paper. For example: checked specifications developed by process design; matched specifications against requisition, purchase order and service level agreement (SLA). All match: no problem found. It can therefore be concluded that the purchasing function ordered what was specified and the supplier shipped what was ordered in line with the SLA.
Root cause analysis is nothing more than a process of elimination, so it’s vital to remain objective and use thought stimulating tools like mind mapping and the five whys. At the end of this fact finding exercise, the team will know exactly what processes related to this situation are acceptable and which ones have problems. By following the trails, the root cause will be identified.
Additionally, any contributing factors or secondary causes will also be uncovered. This allows for the development of a corrective action plan that addresses both the root cause and the ancillary issues that are contributing to it.
It is impossible to develop an effective action plan without thorough root cause analysis. Equally, it is impossible to conduct root cause analysis effectively without implementing it as a controlled process.
Chris Smith, PCQI
Programme Lead, rove.
If you’re interested in studying one of our CQI and IRCA Quality Management courses, you can find out more here.