Dr Genichi Taguchi, born in Japan in 1924, was an engineer and statistician. Taguchi is famous for his pioneering methods of modern quality control and low-cost quality engineering. From the 1950s onwards, Taguchi developed a methodology for applying statistics to improve the quality of manufactured goods and reduce costs, known as the Taguchi Methods. He also developed the quality loss function.
A CONTROVERSIAL APPROACH
The ‘Taguchi methods’ of applying statistical theory to manufacturing problems have raised controversy, their attraction to many people as an engineering tool being counterbalanced by statisticians who are critical of their validity. The controversy relates to Taguchi’s procedures for the statistical design of experiments in furtherance of process optimisation; the objectors claim lack of rigour, lack of originality, lack of accuracy and lack of efficiency. However, in contrast to this this opinion, many more engineers have been trained in and use Taguchi methods than other techniques, even when taught in the traditional way.
1: TAGUCHI METHODOLOGY
Taguchi methodology is concerned with the routine optimisation of product and process prior to manufacture, rather than emphasising the achievement of quality through inspection. Instead, concepts of quality and reliability are pushed back to the design stage where they really belong. The method provides an efficient technique to design product tests prior to entering the manufacturing phase.
However, it can also be used as a trouble-shooting methodology to sort out pressing manufacturing problems. Japanese companies began applying Taguchi methods extensively from the early 1950s, including Toyota and its subsidiaries. His first book, which introduced orthogonal arrays, was published in 1951.
Taguchi breaks down off-line quality control into three stages:
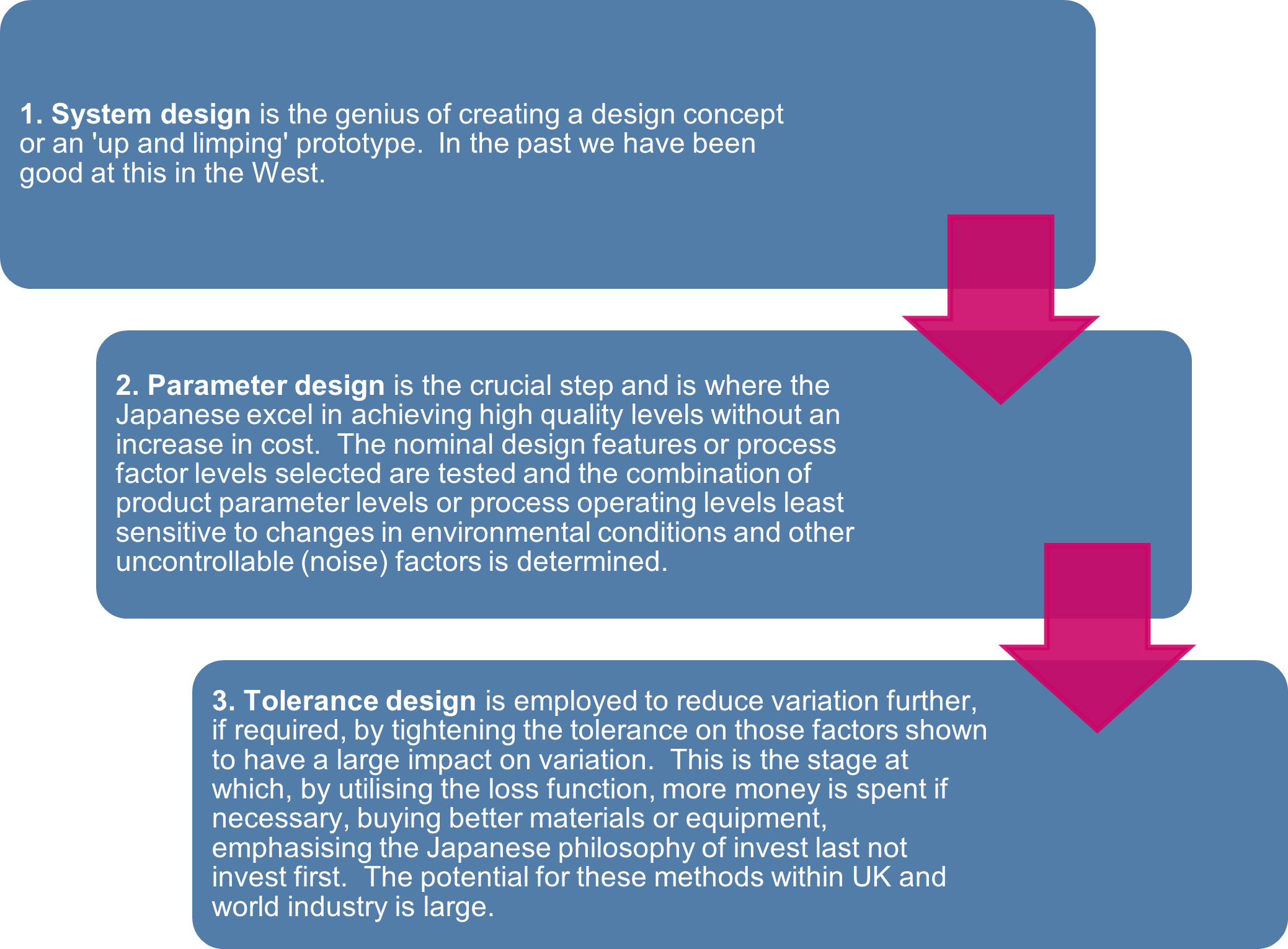
Typically, designs and line calibrations are in reality far from optimal. Much manufacturing folklore is based on the need to ‘twiddle’ important parameters or settings. Typically, we do not understand the correct settings although we do have our prejudices.
Taguchi methodology is fundamentally a prototyping method which enables the engineer or designer to identify the optimal settings to produce a robust product which can survive manufacturing time after time, piece after piece, to provide the functionality required by the customer.
2: TAGUCHI LOSS FUNCTION
TOTAL LOSS TO SOCIETY
An important dimension of the quality of a manufactured product is the total loss to society generated by that product. Taguchi’s definition of (lack of) quality is “The loss imparted to society from the time a product is shipped”. Loss can be one of two things: either loss caused by variability of function (of the product), or loss caused by harmful side-effects.
Traditionally, manufacturing organisations have tended to assume there is no “non-conformance cost” associated with a product which is within its specification limits; they feel costs arise only when out-of-specification product has to be reworked or downgraded. This view is illustrated below. The examples given below disprove this. Note that close control of the process saves a great deal of inspection effort.
COST OF VARIATION – TRADITIONAL MODEL:
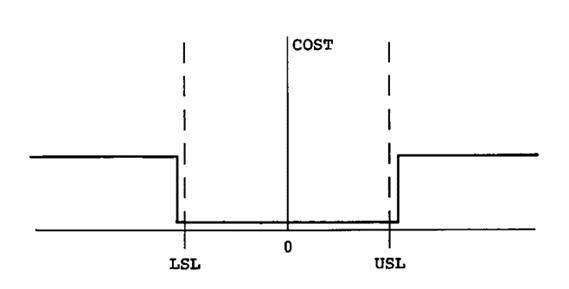
In contrast to the traditional view, Taguchi claims that a quadratic loss function exists, incurring non-conformance costs for anything which deviates to any degree from the design value, and increasing according to the square of the deviation from the desired value. This is shown in the following figure.
COST OF VARIATION – TAGUCHI MODEL:
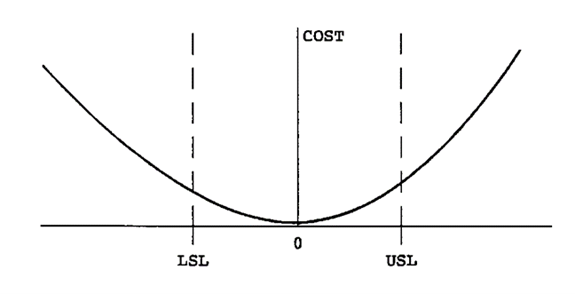
STAYING IN BUSINESS
In a competitive economy, continuous quality improvement and cost reduction are necessary for staying in business.
INCESSANT REDUCTION IN VARIATION
A continuous quality improvement programme includes continuous reduction in the variation of product performance characteristics about their target value. A high-quality product performs near the target value consistently throughout the product’s life and under all different operating conditions.
THE CUSTOMER’S LOSS
The customer’s loss due to a product’s performance variation is often approximately proportional to the square of the deviation of the performance characteristic from its target value.
Traditional inspection has enforced acceptance of product within the specification tolerance, and rejection of product outside the tolerance. This encourages us to think of quality as an all-or-nothing concept. Taguchi’s attitude follows on from the point made under the previous heading; the closer an item is to its design value, the better it will work regardless of where we put the specification limits. The more closely we control the variation the more we can improve the product.
DESIGN AND MANUFACTURE
The final quality and cost of a manufactured article are determined to a large extent by the engineering design of the product and its manufacturing process. Integrated product and process design plays a crucial role in the success of the product; it means designing for manufacturability.
REDUCTION OF PERFORMANCE VARIATION
A product’s (or process’s) performance variation can be reduced by exploiting the non-linear effects of the product (or process) parameters on the performance characteristics.
STATISTICALLY PLANNED EXPERIMENTS
Statistically planned experiments can be used to identify the settings of product (and process) parameters that reduce performance variation. Taguchi has developed an original approach to setting up statistically planned practical experiments to optimise product or process design.
3: ACCOLADES
1960 – Deming Prize for Individuals
1986 – Willard F. Rockwell Medal of the International Technology Institute
1989 – Indigo Ribbon from the Emperor of Japan
1990 – Honoured as a Quality Guru by the British Department of Trade and Industry
1995 – Honorary member of the Japanese Society of Quality Control
1996 – Honorary Fellow of the Institute of Directors (India)
1997 – Automotive Hall of Fame Inductee
1998 – Honorary member of the American Society for Quality
1998 – Honorary member of the American Society of Mechanical Engineers
1999 – Honorary president of the Robust Quality Engineering Society (Japan).
4: FIND OUT MORE ABOUT GENICHI TAGUCHI
The below course considers Genichi Taguchi theories in more depth:
5: FURTHER RESEARCH
If you’re interested in finding out more about Genichi Taguchi click on the links below:
- Watch – Taguchi Contributions to Quality Management
- Read – British Library